2DW23x Zeners and drift (part 7)
February 16, 2017
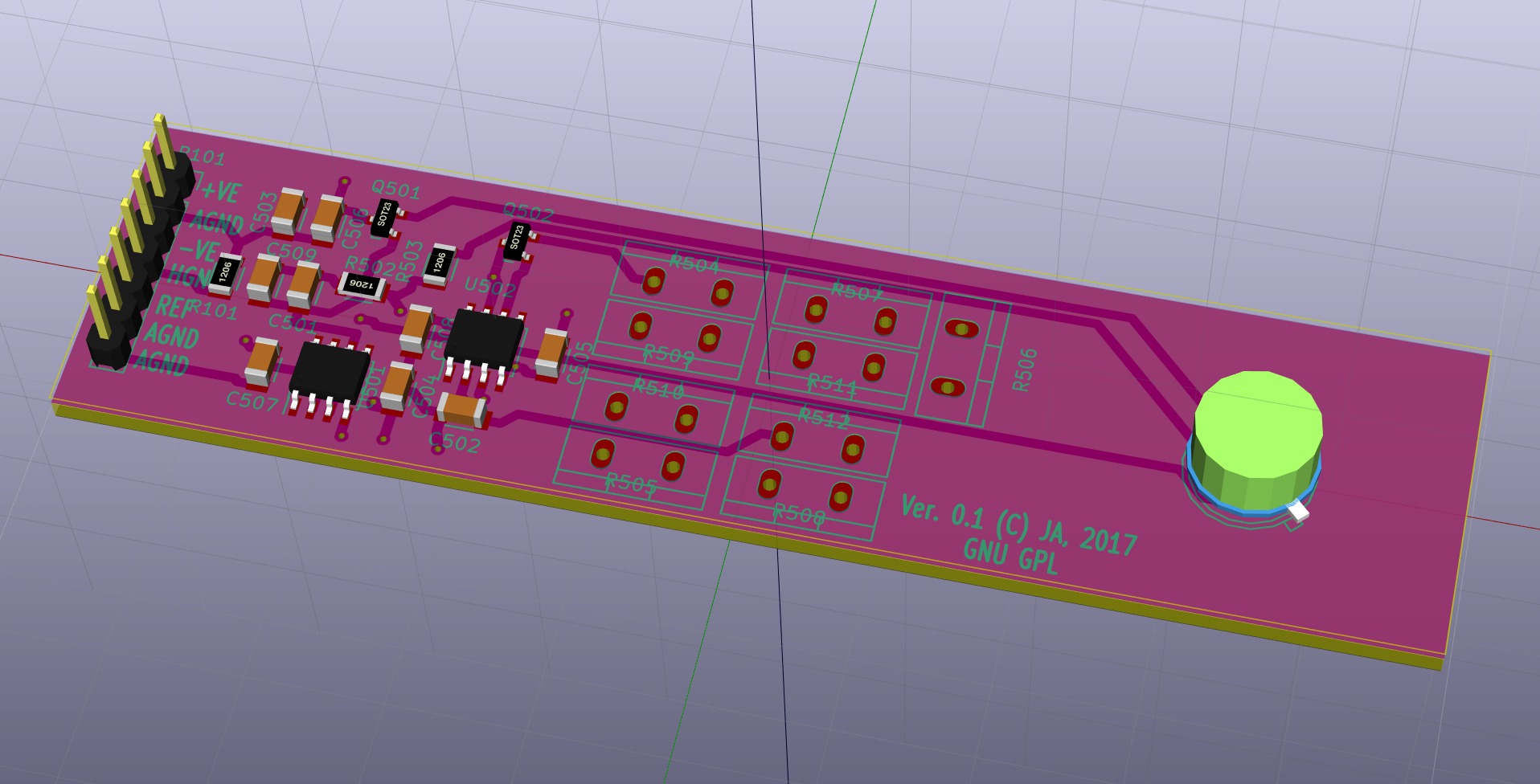
The current unknown for the 2DW23x is drift performance over time.
Using Kicad, I created a basic four-layer PCB that should be a more robust for some longer-term experiments than the perfboard implementation.
Board features
- Trimpots have been eliminated due to their continued poor performance. Instead, dividers can use up to four resistors for current adjustment. For example - two main resistors (5.1k/10k) and one or two smaller values for fine-adjustment. Initial trim setup can still use a pot - in order to determine values based on variation in 2DW23x TC0 current.
- extra pads to parallel the capacitors in the heater loop. Although a single 10uF ceramic should be enough.
- a 0 ohm resistor to connect Heater GND with Analog GND at the pin headers
Random thoughts
- It would be really nice if the TC0 current could be set, so that the op-amp output was close to 10V
- Vishay z201 foil resistors with 0.2ppm/C tempco will probably be used for the main dividers. Trimming will be done with s102 or ptf56 for the better range of resistor values
- I have chosen to avoid placing the resistors on a temperature-stable carrier together with the 2DW23x zener. First because of the more complex assembly. Also, looking at the z201 tempco charts reveals second-order effects increase as temperature moves away from 25C, figure 1 pdf. So, although a carrier would provide better thermal stablility, it’s not for free at the higher temperature set-point. There is also the possibility of unknown temperature gradients across the carrier unless other measures were adopted.
- It will be interesting to see what effect (if any) radiant heat from the 2DW23x case will have on the nearby resistors.
Peliter devices?
I found a source for some minature peltier coolers. In this case the 200ohm heater-resistor bonded to the bottom of the 2DW232 case could be replaced by a Peltier cooler with sufficient power to balance the heat generated by the zener current. It would be possible to set the regulation temperature to co-incide with expected room temperature - say 23C.
Advantages
- less thermal stress on the 2DW23x when cycling between use and non-use. Reduced hysteresis issues. Also between the time that the part is manufactured and the time that it is deployed/used.
- It feels elegant to balance the heating effect from the 20mA zener current with a cooling loop. At the moment there needs to be enough headroom above the ordinary heated temperature for the temperature regulation loop to have room to work in various ambient settings.
- lower thermal gradients over the device - because the setpoint is closer to ambient temperature.
- More ammenable to the carrier board solution - to keep the precision resistors at the same temperature as the 2DW23x. This is because of the lower second-order TCR affects of the Z201 around 25C already mentioned.
Disadvantages
- Is it over-complexifying the design, and assembly?
- The poor power efficiency of Peltier devices is discouraging. But if we accept that the reference is already high-current then it seems less of an issue.